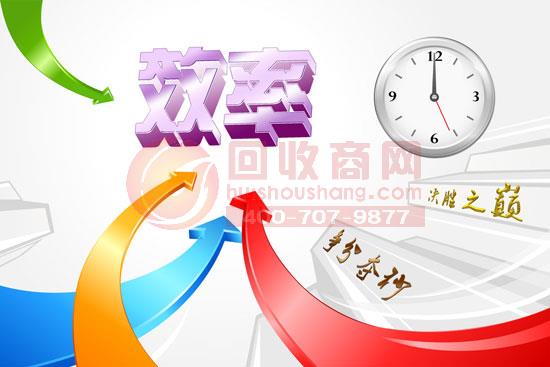
在实际生产过程中,我们会发现相同的数控机床不同的人员操作, 在相同的工作时间内生产效率相差很大,许多数控机床的加工能力得不到充分的体现,发挥不出其最佳作用。据调查,数控机床的实际切削时间不到工作时间的60%,造成极大的浪费。而影响数控机床加工效率的因素很多,也很复杂。我在实际加工中发现,事实上数控机床的生产效率可以提升的空间是很大的,影响数控机床生产效率主要有以下几方面因素,在使用过程中,只有充分考虑影响数控机床生产效率的各方面因素,想方设法地提高数控机床的生产效率,才能使数控机床的生产能力得到充分的发挥。
1.制订合理的加工工艺路线,减少数控铣削的辅助时间
为了提高数控机床的生产效率,首先必须认真分析数控机床所加工的 零件,弄清零件的材料、结构特点和形位公差要求、粗糙度、热处理等方面的技术要求。然后在此基础上,选择合理的铣削加工工艺和简洁的加工路线。
加工工艺的制定:通常一个零件可以有数种不同的工艺过程,零件的工艺过程不同,其生产效率、加工成本以及加工精度往往有着显著的差别,因此我们应在保证零件加工质量的前提下,根据生产的具体条件,尽量提高生产效率和降低生产成本,制定出合理的加工工艺。 加工路线的确定:正确简洁的加工路线,是保证加工质量和提高效率的基础。选择零件的加工路线时,必须遵守加工路线的确定原则,才能达到提高生产效率的目的。确定加工路线的原则主要有:应能保证零件的加工精度和表面粗糙度的要求,且效率较高;应尽量使加工路线最短,这样既可减少程序段,又可减少刀具空程走刀时间;应使数值计算简单,程序段数量少,以减少编程工作量。此外,确定加工路线时,还要考虑工件的加工余量和机床、刀具的刚度等情况,确定是一次走刀,还是多次走刀来完成加工。同时,应尽量做到一次装夹、多方位加工,一次加工成形。这样,可减少工件的安装次数,有效缩短搬运和装夹的时间。这样,既能有效地提高加工效率又能很好地保证零件的位置精度要求。
2.选择恰当的刀具,提高数控铣床的切削效率
选择刀具应考虑数控机床的加工能力、工序内容、工件材料等因素。 数控机床所选择的刀具,不仅要求具有高硬度、高耐磨性、足够的强度和韧性、高耐热性及良好的工艺性,而且要求尺寸稳定、安装调整方便。所以应尽量采用新型优质材料制造数控加工刀具,并优化刀具参数,使刀具的尺寸与被加工工件的表面尺寸和形状相适应。那么,怎样选择合适的切削刀具呢?
(1)选择适当的刀具
在数控机床的切削加工中,金属切削刀具的作用是极其重要的。制造刀具的材料必须具有较高的硬度、耐磨性和耐热性,足够的强度和韧性,良好的导热性及工艺性,并具有较好的经济性。在选用刀具过程中,在满足零件加工要求的前提下,尽量选择直径较大的刀具,它的强度及韧性较好;同一道工序中,选用的刀具数量尽量少,以减少换刀次数;尽可能选择通用的标准刀具,不用或少用特殊的非标准刀具。
(2)合理确定对刀点
对刀点是在数控机床上加工零件时,刀具相对于工件运动的起点。又称“程序起点”或“起刀点”。对刀点的选择必须遵守以下原则:便于用数字处理和简化程序编制;在机床上找正容易,加工中便于检查;引起的加工误差小。对刀点的位置可选在工件上,也可选在工件外面(如夹具或机床上),但必须与零件的定位基准有一定的尺寸关系。对刀点应尽量选在零件的设计基准或工艺基准上,如以孔定位的工件,可选孔的中心作为对刀点。刀具的位置则以此孔来找正,使“刀位点”与“对刀点”重合。这样,可以便可以更好地提高对刀的效率,保证加工质量。
3.合理安装夹紧工件,提高装夹速度
在数控机床上加工工件时,工件的定位安装应力求使设计基准、工 艺基准与编程计算的基准统一;尽量减少装夹次数,尽可能在一次定位装夹后,加工出全部待加工表面;避免采用占机人工调整式加工方案,以充分发挥数控机床的效能。
数控机床切削加工时,对零件进行定位、夹紧设计以及夹具的选用和设计等问题上要作全面考虑。在设计选择夹具时,首先要保证夹具的坐标方向与机床的坐标方向相对固定。其次,要协调零件和机床坐标系的尺寸关系。